How Do I Troubleshoot Common Machinery Issues
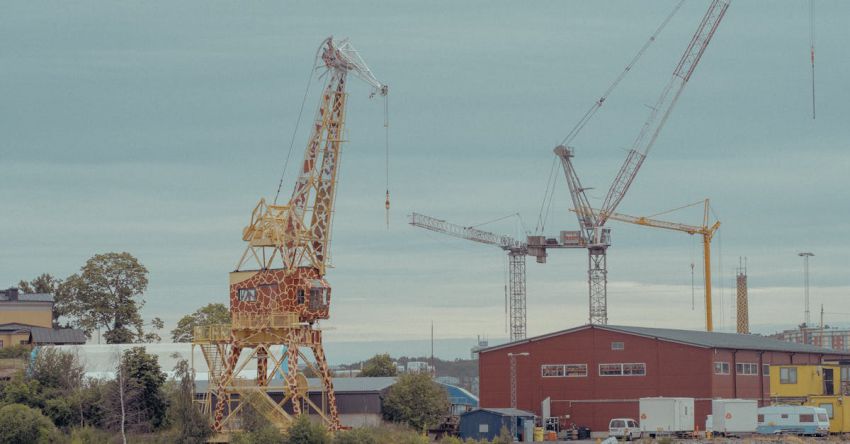
Machinery plays a vital role in various industries, from manufacturing to construction. However, encountering issues with machinery is not uncommon and can disrupt operations, leading to downtime and loss of productivity. Knowing how to troubleshoot common machinery issues can help minimize these disruptions and keep operations running smoothly.
Identifying the problem
When faced with machinery issues, the first step is to accurately identify the problem. This requires a keen eye for detail and a systematic approach. Start by observing the machine in action and listening for any unusual sounds or vibrations. Check for error messages on the display panel or any visible signs of damage or wear. Understanding the symptoms of the issue is crucial in determining the root cause.
Checking for power supply
One of the most common reasons for machinery malfunctions is a power supply issue. If the machine fails to turn on or operates intermittently, the problem might lie in the power source. Begin by checking the power cord for any damage or loose connections. Ensure that the machine is plugged into a functioning power outlet and that the circuit breaker has not tripped. If the machine runs on batteries, make sure they are adequately charged or replace them if necessary.
Inspecting for blockages
Another frequent issue that machinery faces is blockages in the system. Whether it’s a clogged filter, jammed conveyor belt, or obstructed ventilation, blockages can impede the machine’s performance. Inspect the various components of the machinery for any obstructions and clear them out carefully. Regular maintenance, such as cleaning filters and lubricating moving parts, can prevent blockages from occurring in the future.
Checking for leaks
Leaks are a common problem in hydraulic systems and can lead to a loss of fluid and pressure, affecting the machine’s operation. Inspect the hydraulic hoses, fittings, and seals for any signs of leakage. Address any leaks promptly by tightening connections or replacing damaged components. Regularly checking for leaks and maintaining proper fluid levels can prevent costly repairs and downtime.
Calibrating sensors and controls
Machinery often relies on sensors and controls to operate efficiently. If these components are not properly calibrated, it can result in inaccurate readings and performance issues. Check the calibration of sensors, gauges, and control panels to ensure they are functioning correctly. Recalibrate as needed according to the manufacturer’s specifications to maintain accuracy and consistency in the machine’s operation.
Testing safety features
Safety features are critical in machinery to protect operators and prevent accidents. If safety mechanisms, such as emergency stop buttons or safety guards, are not functioning correctly, it can pose a significant risk to personnel and equipment. Regularly test these safety features to ensure they activate as intended in case of an emergency. Replace any faulty components and provide adequate training to operators on their proper use.
Conducting regular maintenance
Preventive maintenance is key to avoiding unexpected machinery breakdowns. Establish a maintenance schedule and adhere to it diligently to keep machinery in optimal condition. Regularly inspecting, cleaning, and lubricating components can extend the machine’s lifespan and reduce the likelihood of costly repairs. Keep detailed maintenance records and address any issues promptly to prevent them from escalating.
In conclusion, troubleshooting common machinery issues requires a systematic approach and attention to detail. By identifying problems early, addressing them promptly, and conducting regular maintenance, you can keep machinery running smoothly and minimize downtime. Stay proactive in monitoring machinery performance and prioritize safety to ensure efficient operations and prolong the lifespan of equipment.